CLEANING TO EXACTING STANDARDS

Precision Cleaning means cleaning to very exacting standards, with very low tolerance for left-over microscopic (<0.3 microns) particles or other contaminants. Components requiring the most stringent cleanliness standards are processed in heavily regulated environmental conditions that are similiar to those that the components operate in.
In many high-tech precision industries, precision cleaning is a prerequisite for newly-manufactured parts prior to assembly, this delicate process is also a routine maintenance activity that prevents particle contamination on valuable products that can be costly as well as disruptive.
Electronics Manufacturing related services & products:
- Precision Cleaning and process deposition removal via:
- Spray cleaning, immersion cleaning and ultrasonic cavitation and implosion
- 24/7 process-kits recycling management
- Specialized thermal spray coating on new or re-used components
- Class 1000 and 100 cleanroom packaging
- Surface profiling for contaminant adhesion
Serviced Electronics Manufacturing equipment:
New and used process components and assemblies, such as shields, platens, stainless liners, shutters, process chamber doors, transfer plates, rotating drums, process chambers, box coaters, CVD and PVD parts, load lock chambers, shielding, valves, ion sources, diffusion pumps, ion pumps, wave guides, etc.
Frontken Offers the following range of Precision Cleaning Processes:
Precision Pico-Cleaning
Precision Pico-Cleaning can be defined as the removal of pico-level (below one nm) contamination or unwanted material or particles from a surface (unwanted material deposited on, or attached to a surface)—for ultra-high vacuum applications in semiconductor manufacturing.
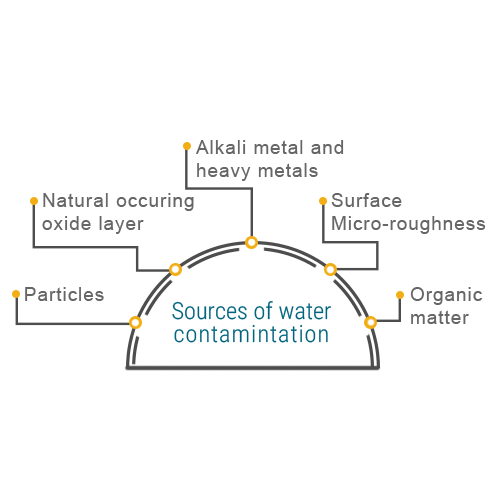
Effective precision cleaning and surface preparation has been pivotal and the most common operation in the semiconductor manufacturing. However, the cleaning applications in the semiconductor manufacturing are tougher to meet as nano-contamination control requirements increase, device dimensions decrease, material removal limits reduce, and three dimensional nano-scale features become more common. Advanced Precision Pico-Cleaning is one of the major factors which will caused a large impact on Productivity, Defects and Contamination for all semiconductor manufacturing from PVD, to Etch, to Diffusion and related processes.
The uniqueness of Frontken Pico-cleaning process relies on the optimal combination and effectiveness of both physical and chemical removal mechanisms together with advanced metrology and data analytics. The final baseline results on the process kits show substantial contaminants removal efficiency of up to 100 percent.
Frontken has an Advanced Laboratory for Research and Development equipped with Advanced Metrology and Measurement Capability; and has been continuously working on “advanced generation” cleaning, coatings and materials for the 7nm technology node and below.
Frontken Advanced Precision Pico-Cleaning Technology
(a) Physical and Mechanical Methods: Ultrasonic and/or megasonic/gigasonics; CO2 Techniques; sublimation; thermal shock and the air pressure; High and low pressure water gun; thermal decomposition; vacuum Oven bake; laser and/or Plasma conditioning; photodecomposition; Vacuum oven up to 1,600 deg C or higher; Filtered N2 or dry air gun flow; grit or bead texturing; polishing techniques, etc.
(b) Chemical Methods: liquid-chemical ablation; Ammonia and hydrogen peroxide mixtures (APM); C3 Mixed Acids; IPA; C3H6O; CH3COCH3; CH3COOH; Tetramethyl; citric acid; C2H2O4; tartaric acid; and other organic reagents, etc; other Strong oxidizer to break organic bonding and also reacts with metals and metal ions to form high valence state, etc.
Summary of Products and Services
Core Products and Services can be summarised as follows:
- Scope of Work – Parts Clean + Parts refurbishment + Parts Management.
- Provide Advanced Total Solution for critical chamber’s components recycle cleaning, re-coating, repair, refurbishment, recovery. (28nm, 22/20nm, 16/14nm, 10nm, 7nm, 5/3nm ready).
- Provide Advanced Precision Chemistry Cleaning Services (28nm, 20nm, 16nm, 10nm, 7nm, 5nm ready).
- Provide Complete proprietary advanced coating using Robotic HVOF, Plasma and TWAS Coating services. Advanced coatings include specific metal oxides, YSZ, Yttria Y2O3, Alumina Al2O3, customised triphase oxide, SiO2, ACME, PBC, etc;
- Provide complete fully automated type II/III hard anodizing process with proprietary multi-mixed acid electrolyte and optimized operating parameters for 6000 series high purity alloy and related materials. Other advanced surface metamorphosis include electroless nickle plating, selective nickle plating, laser, etc.
- Provide Joint (customers and OEM Partners) innovative technology development and support for improving critical chamber components performance and life time extension, zero-contamination on process kits and lower total cost of tool ownership.